Waterworks Joints 101
There are many different joints that can be found on waterworks pipeline components. Some are specific to pipe material, some are specific to application, others can be specific to a manufacturer.
The three most common joints that are the focus of this discussion (flange, mechanical joint, and push-on joint) are governed by ANSI/AWWA C111/A21.11 “Rubber Gasket Joints for Ductile Iron Pipe and Fittings” and ANSI/AWWA C900 “Polyvinyl Chloride (PVC) Pressure Pipe and Fabricated Fittings, 4 In. Through 60 In. (100 mm Through 1,500 mm).Flange Joints
There are many different flange configurations available with many different pressure ratings, flange materials, temperature ratings, bolting configurations, and flange facings. Most of these variations come from industrial applications that have very different requirements compared to those of waterworks piping (See Connections Bulletin FL-01 “What is the Pressure Rating of that Flange?”). FL-01 Connections Bulletin "What is the Pressure Rating of that Flange?"
The subject flange is described in AWWA C111 and other AWWA standards covering fittings and other pipeline appurtenances. While the term “Class 150” is commonly used to describe details of the flange, it is not the pressure rating of the flange. Ductile iron pipe and fittings usually have a pressure rating of 350 psi with a “Class 150” flange. Other appurtenances can have the same flange connection with a lower pressure rating because of other aspects of the specific components, but the pressure ratings are usually not dictated by the flange. Also, while this flange is made of ductile iron, it is compatible with many flanges used with steel pipe as well.
Flanged fittings and appurtenances are typically provided with the flanges cast as an integral part of the unit. Flanged ductile iron pipe can be provided and those flanges are usually attached with a threaded connection between the pipe and flange. The seal of the flange joint is usually achieved by compressing a rubber gasket between the flat faces of the mating flanges. The compression comes by tightening the flange bolts. This joint can be seen in cross section in the following illustration.
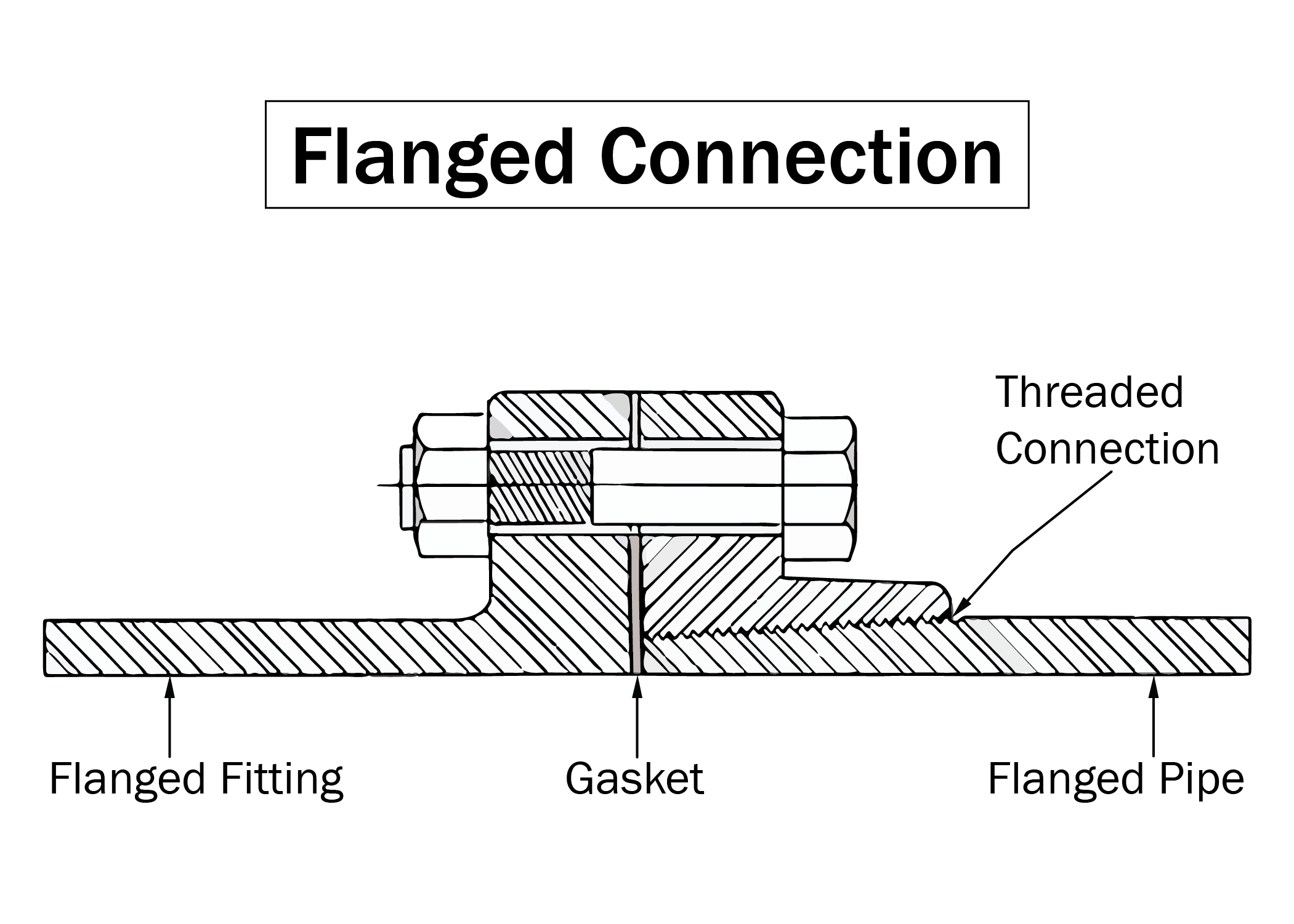
There are many different styles of gaskets for the flanged joint to meet a number of different requirements. For example, some seals facilitate a more reliable seal, some electrically isolate one flange from the other, and others can provide allowance for angular misalignment.
While flanged connections are quite strong, they are also rigid by nature. This aspect can be beneficial when used in above- ground applications such as plant piping. As a result of the rigid nature, this joint is very sensitive to proper alignment and will not allow for parallel, angular, or rotational misalignment. Finally, there is generally the need to install dismantling joints in a flanged system to facilitate disassembly and, occasionally, misalignment. These aspects are also why the joint is rarely used below ground.
The standard flange joint does not lend itself to simple changes in the field. This requires the use of a flange coupling adapter (FCA). A typical FCA has a flange on one side and a compression seal on the other. The compression joint on the FCA is unrestrained. There are a number of restraining options including external rods, special pin arrangements, and restrained flange coupling adapters (RCFA). The EBAA Iron Megaflange RCFA is shown in the following cross section.
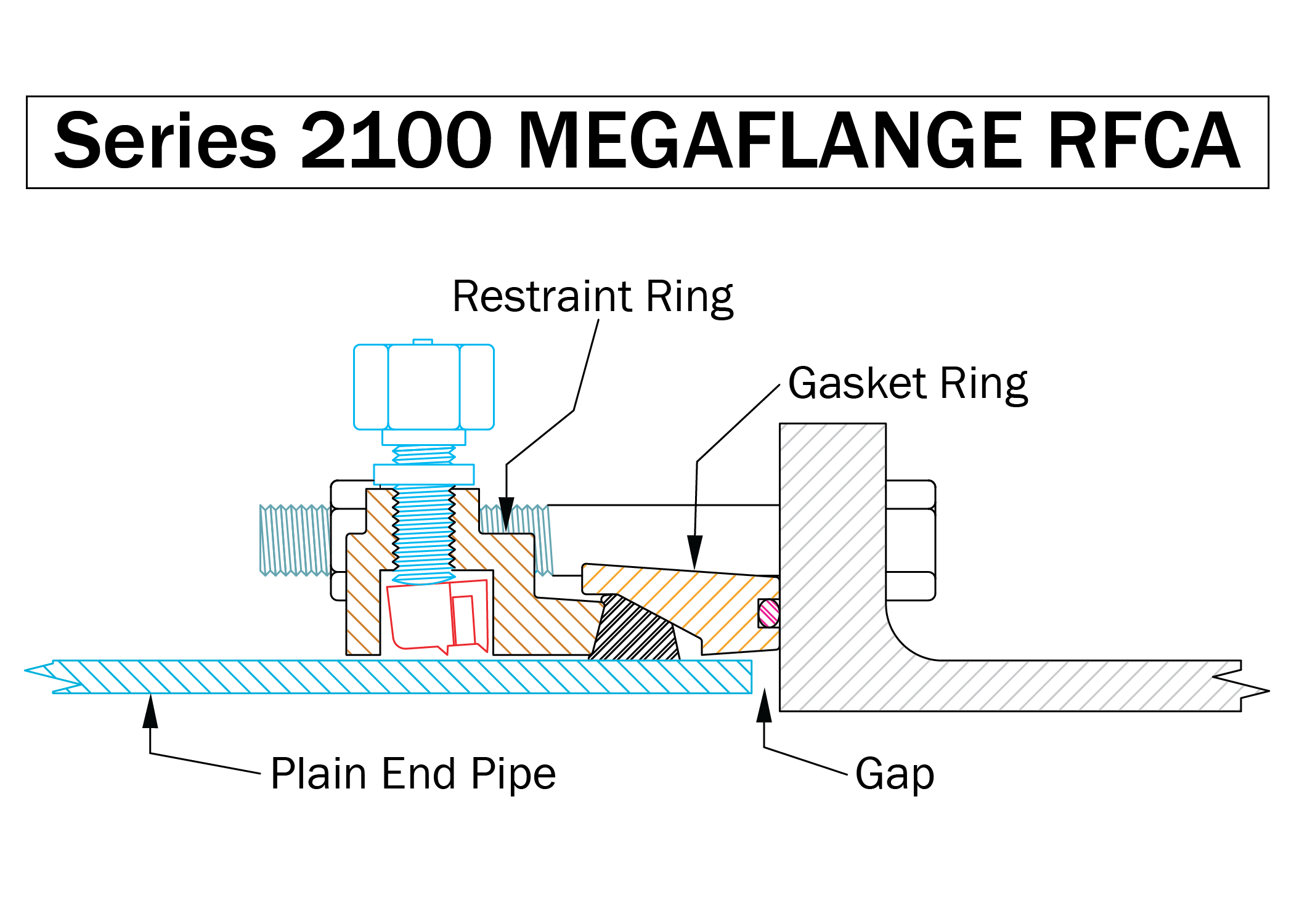
Use of an RCFA allows a plain end pipe to be connected to a standard flange. The pictured unit also allows for joint deflection, length adjustment, disassembly, and use on iron, steel, or plastic pipe.
AWWA flanged fittings are standardized and produced by a number of manufacturers. Flanged pipe is made by several pipe manufacturers and after-market pipe fabricators.
Mechanical Joints
The mechanical joint (MJ) is the most common fitting joint in the American waterworks market. The joint was invented by WD Moore in the 1920s as a means of sealing cast iron pipe connections in natural gas pipelines. In its current form, the joint is shown in the following illustration.
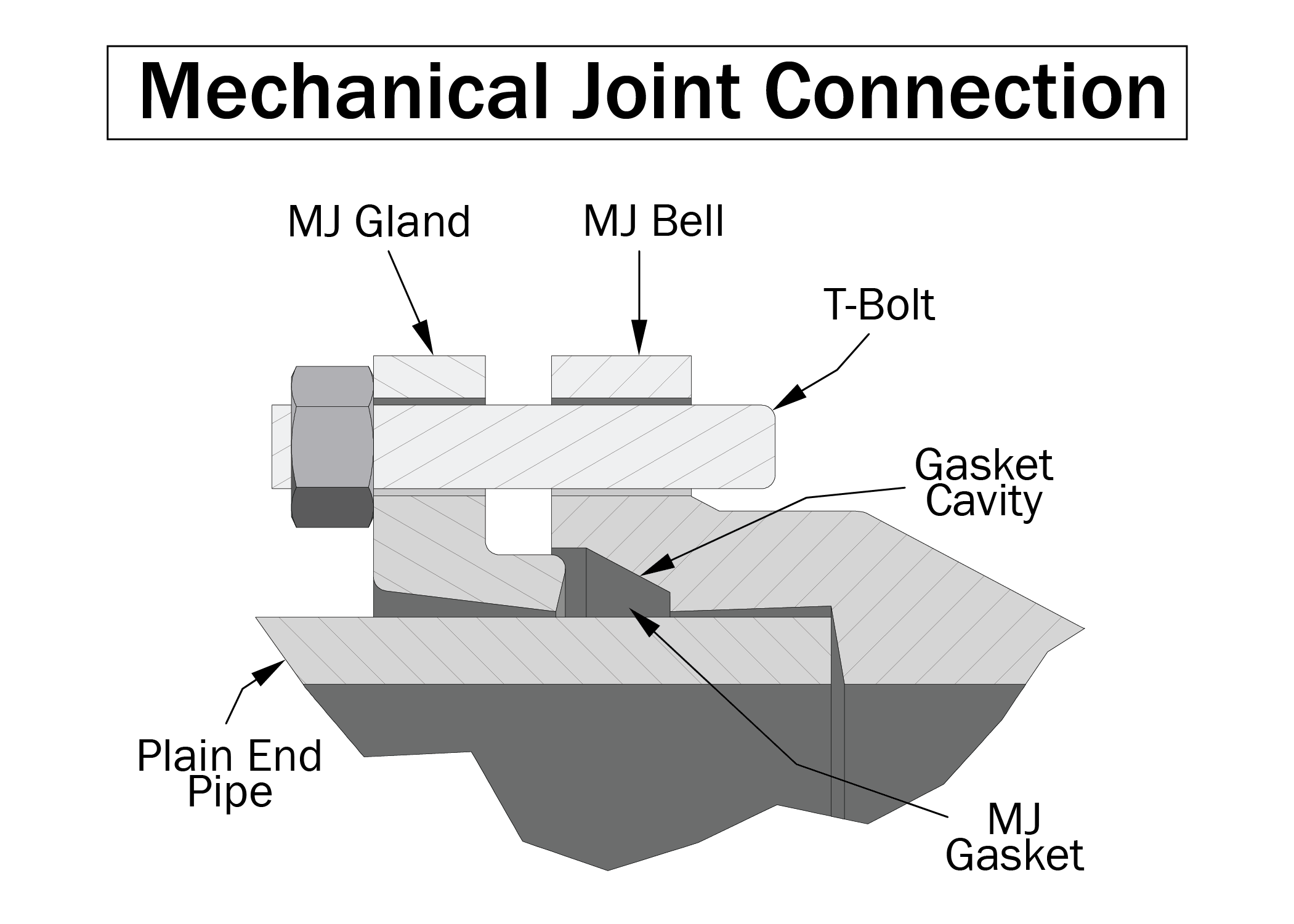
The dimensions of the joint are a part of AWWA C111. This joint can be found on many different pipeline components, even ductile iron pipe. While MJ pipe was readily available many years ago, today it is difficult to obtain.
This joint is very versatile in that it can be used with ductile iron pipe, PVC pipe, PVCO pipe, and ductile diameter HDPE pipe (HDPE use requires an internal stiffener) with a standard gasket. With a transition gasket, the joint can be used with steel pipe and PVC and HDPE (again, with a stiffener) with steel pipe ODs in sizes twelve-inch and below.
The MJ is very field adaptable and that is one of the reasons that it is a very popular joint for fittings and appurtenances. It is a simple matter to cut the pipe and assemble the joint. There is no need for modifying the cut pipe end. Additionally, the installation (which can be found in several AWWA standards as well as manufacturers’ instructions) is very straight forward. In summary, the steps required are
- Make sure all of the components are clean
- Slide the gland onto the end of the pipe
- Lubricate the gasket, inside and out, and slide it onto the end of the pipe
- Push the pipe into the MJ socket, push the gasket into the gasket cavity, and press the lip of the gland against the gasket
- Insert the T-bolts and place the nuts on the threaded end of the bolts
- Tighten the T-bolts until all of the nuts are snug
- Deflect the joint as needed
- Tighten the T-bolts to the recommended torque range (this may require several rounds of tightening, especially in the larger sizes)
The standard mechanical joint is not restrained, but there are many different restraint options on the market. The restraining mechanisms are generally incorporated into the design of the gland, but they can also be a ring separate from the gland that is connected to the sealed joint via extra length bolts. EBAA Iron MEGALUG restraints for ductile iron pipe and PVC pipe are shown in the following illustrations.
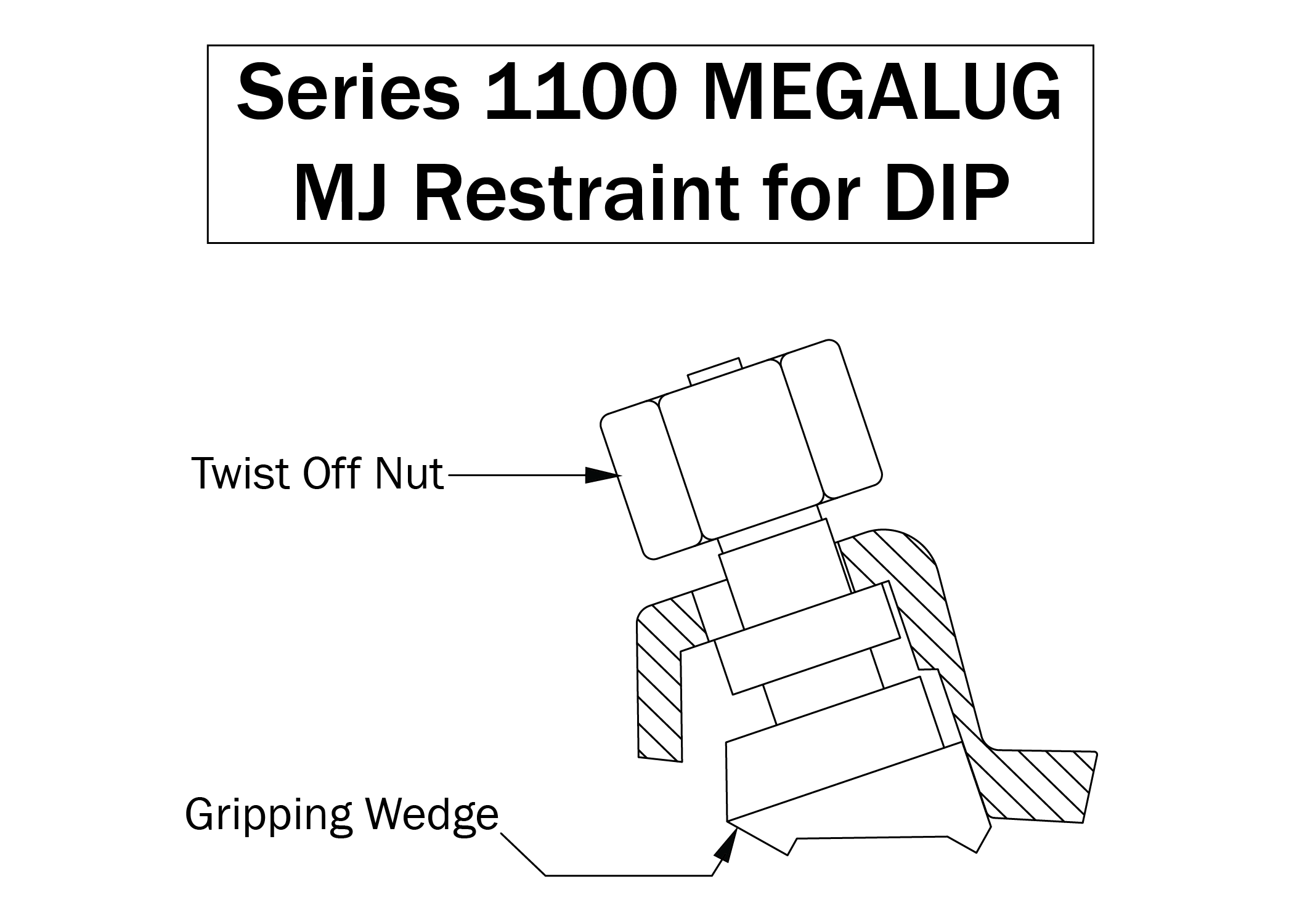
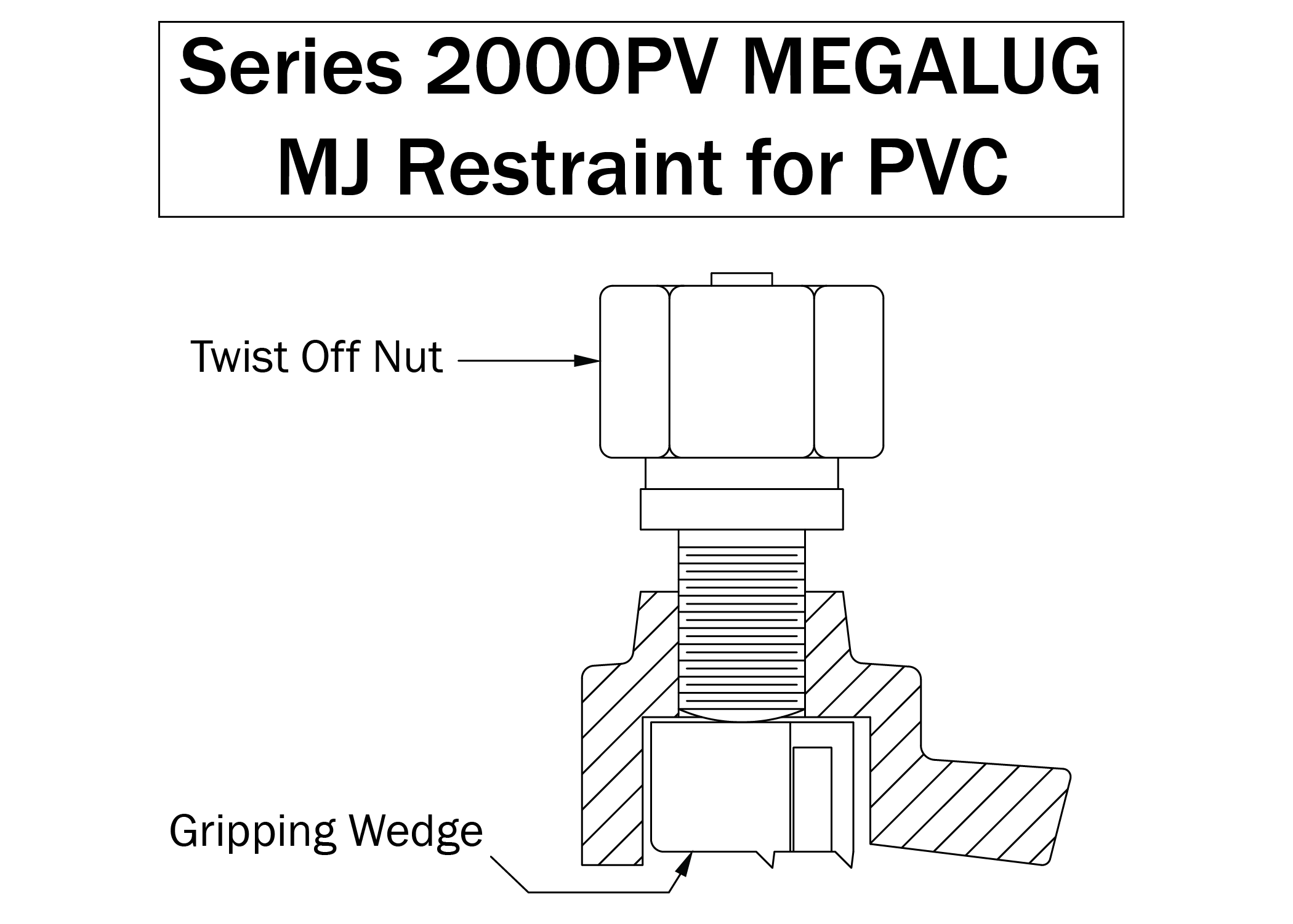
While the majority of MJ connections are used underground, the joint can be used above ground as well.
There are many manufactures that supply fittings, valves, and other appurtenances with MJ connections.
Push-On Joint
The modern push-on joint was developed in the 1950s and is a descendent of the Roll-On Joint. It is, by and large, the preferred pipe-to-pipe joint. Cross sections of typical joints for ductile iron and PVC pipes are shown in the following.
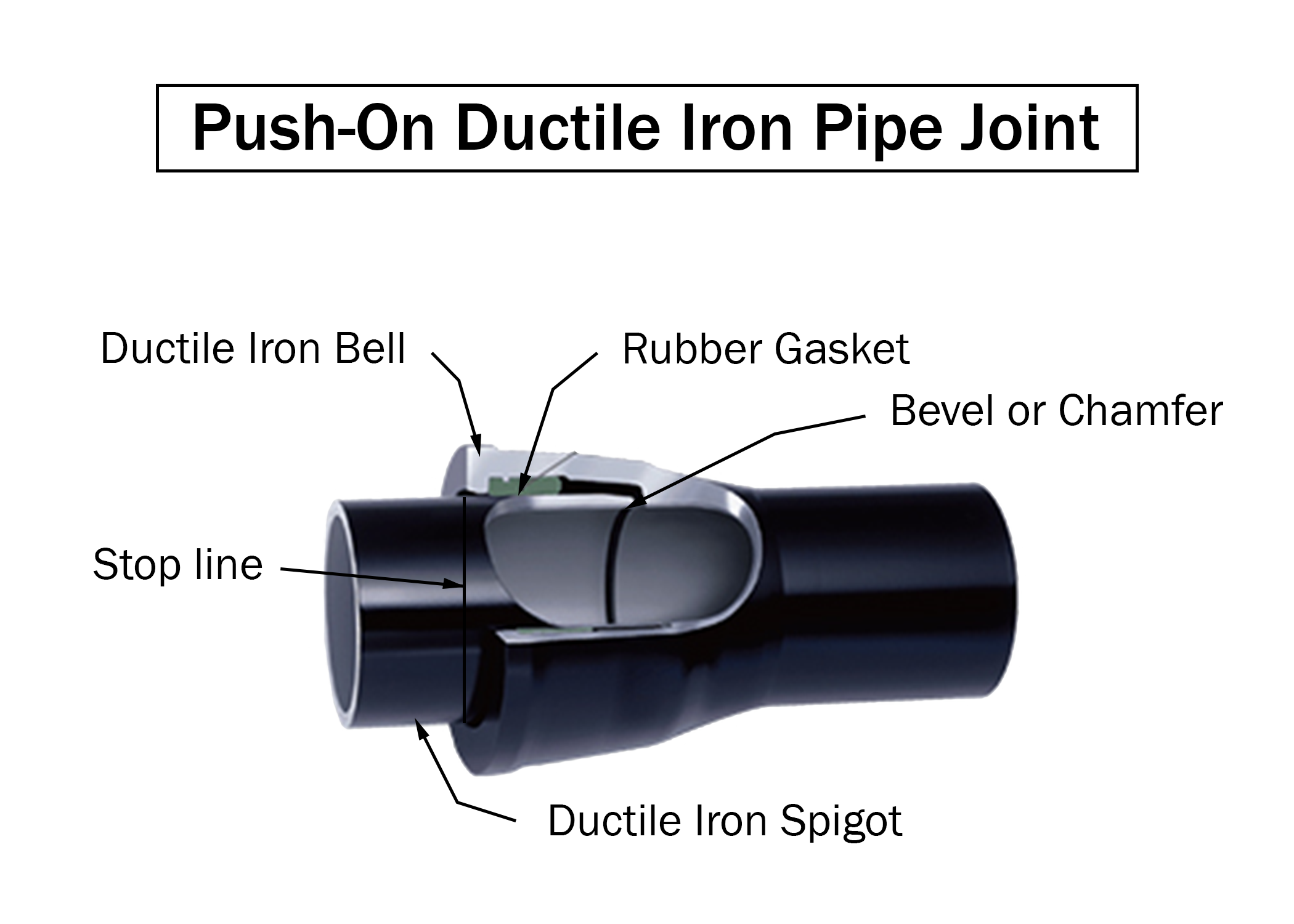
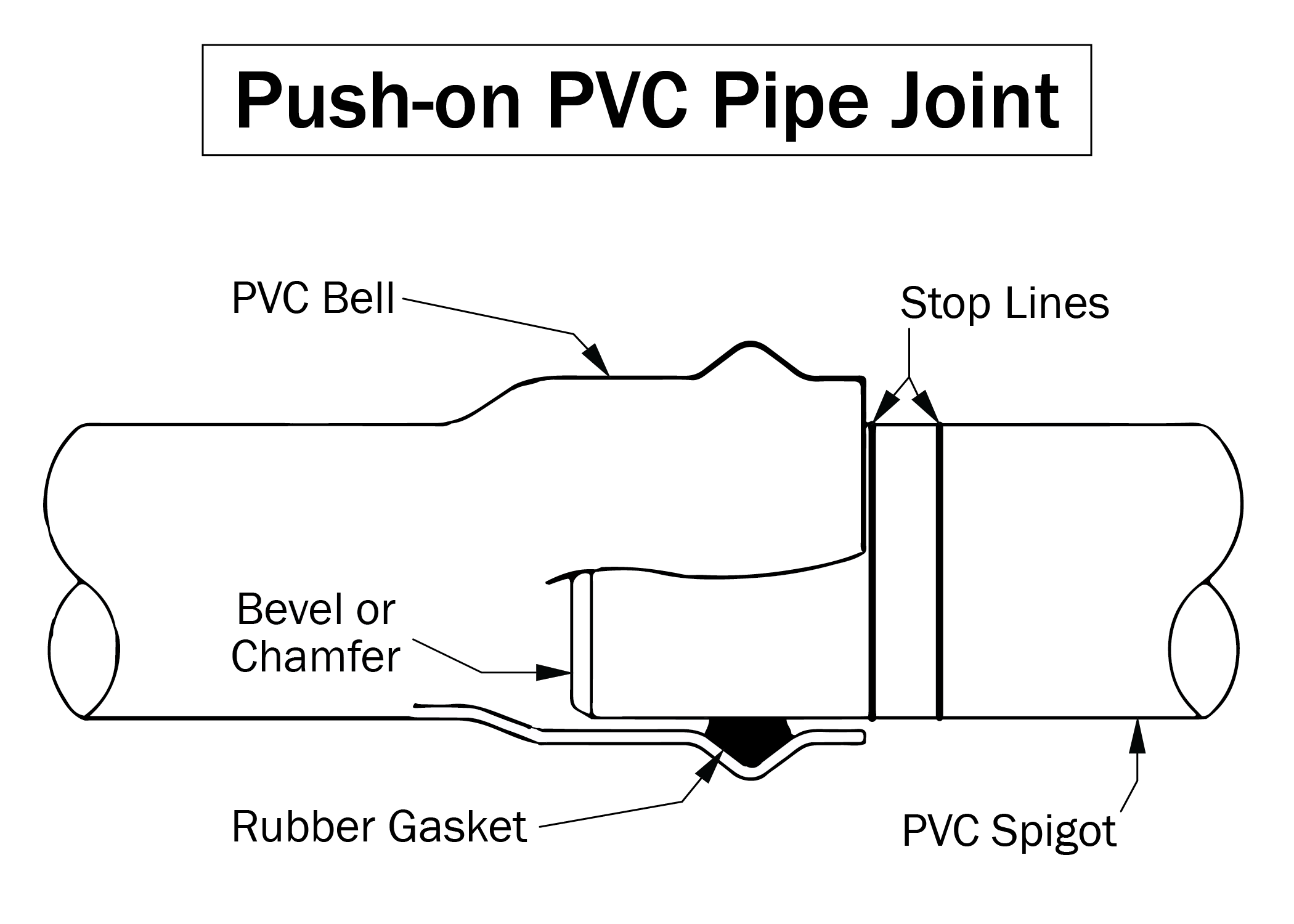
Instructions for the proper lubrication of the of the gasket/spigot are provided by the manufacturer. The installation is completed by pushing the spigot into the bell to the specified depth that is indicated by a line on the spigot. While it is possible to field cut the pipe, the end of the spigot must be chamfered or beveled so that the end of the pipe can gradually deflect the sealing portion of the gasket during the insertion process. The pipe must be chamfered to the dimensions dictated by the pipe/fitting manufacturer. If the pipe end is not chamfered properly, the gasket can become dislodged or be cut and cause leakage. It is also important that the spigot of the joint not be over-inserted or pushed past the stop line. Doing so will limit the deflection capability of the joint, inhibit the ability of the joint to expand and contract, and possibly damage the pipe.
Fittings and appurtenances are available from many different manufacturers. However, as a result of the installation technique, fittings can be difficult to assemble correctly
The standard push-on joint is an unrestrained joint but there are many restraint options available. The standard push-on joint can be restrained with external restraints such as these shown below.
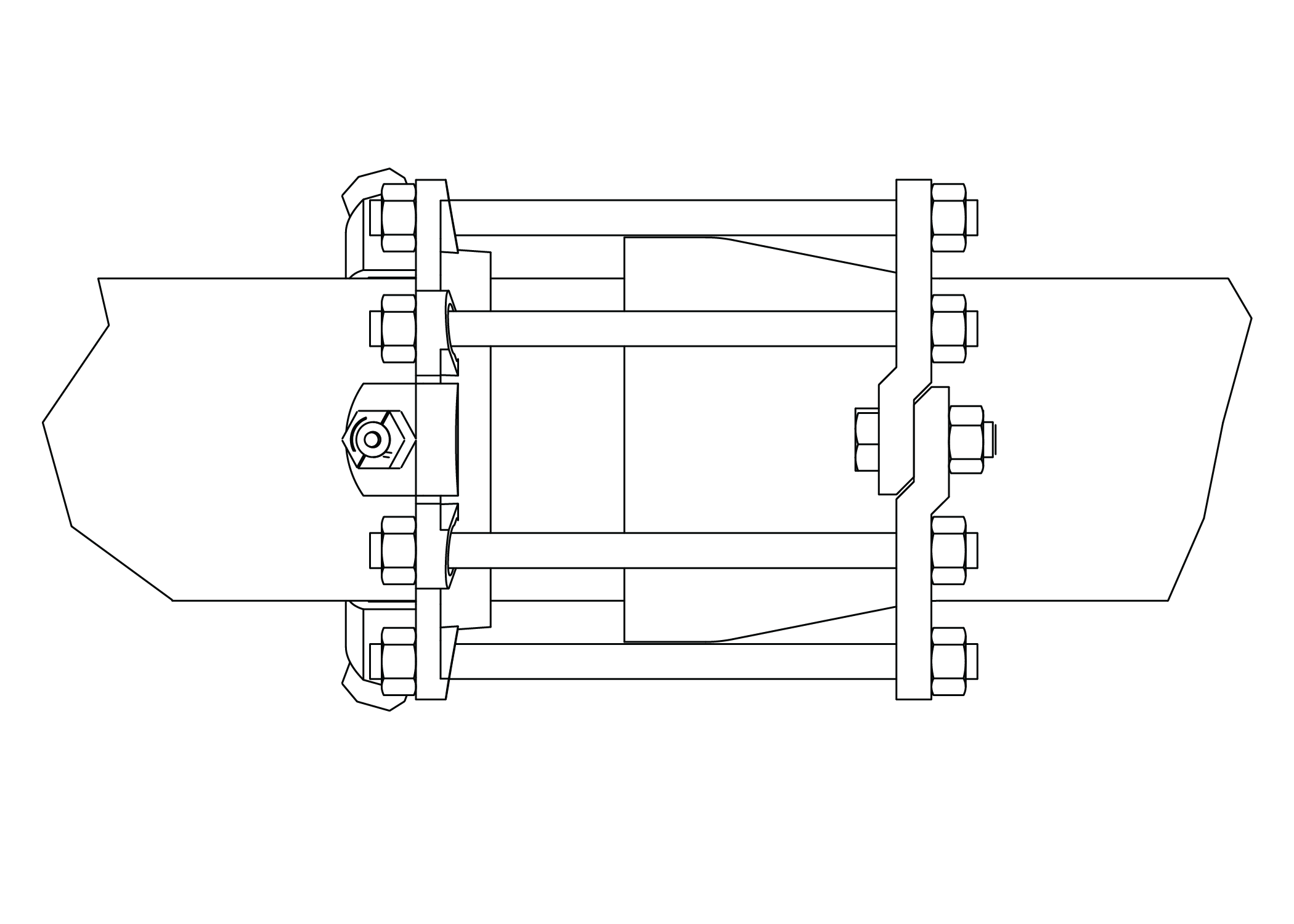
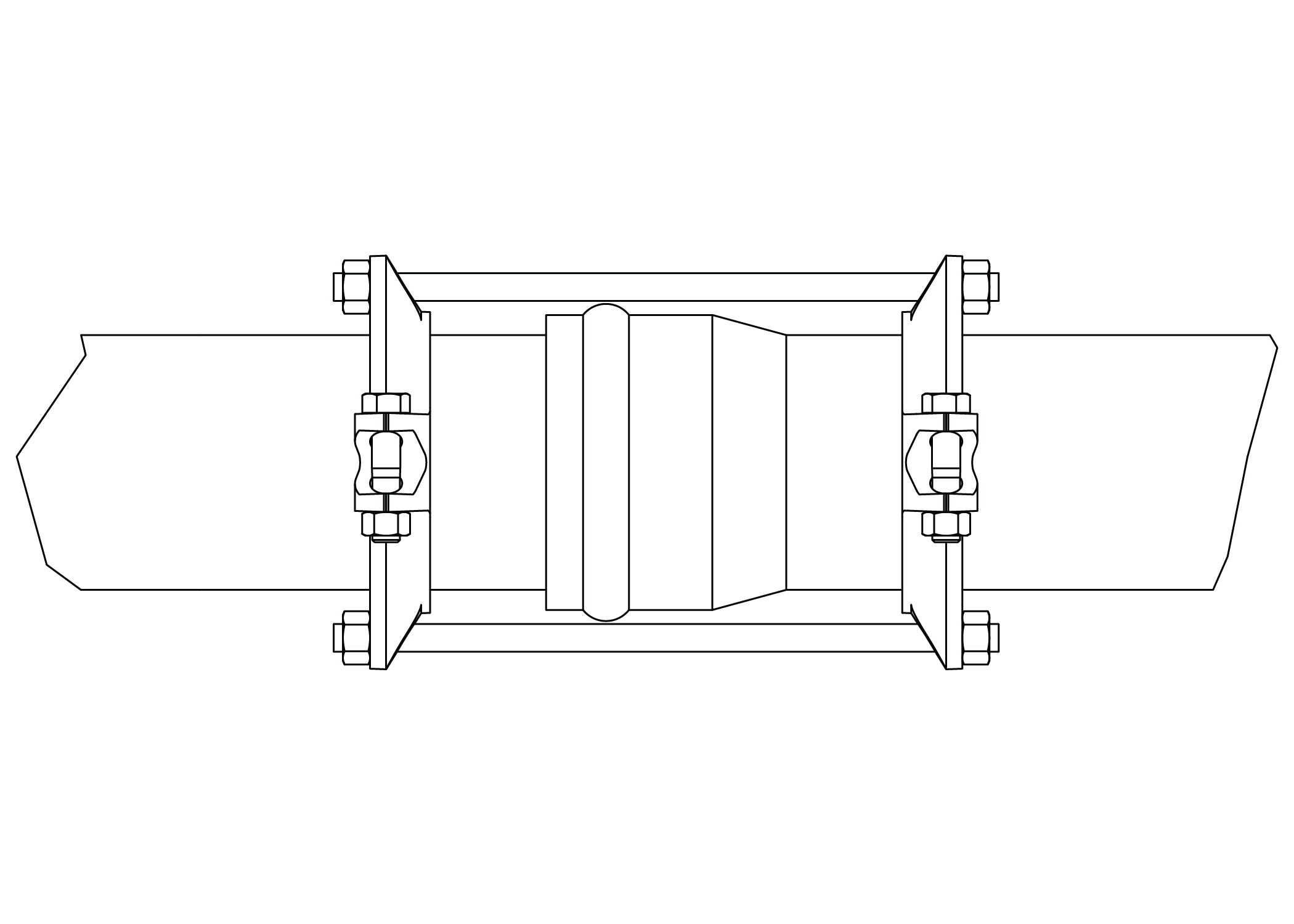
As with the MJ, the joint is commonly used in underground installations but can be used above ground as well. There are also numerous choices available from different manufacturers that incorporate restraint options into the design of the bell/spigot or gasket.
Conclusion
With all pipeline joints, it is imperative that the pipeline be designed properly. For underground, gasketed joints (MJ and push-on) some means of joint restraint must be employed. One of the oldest ways of doing this is with thrust blocks. However, it is a straight forward process to design pipelines with restrained joints. Support documents and an online calculator can be found Here.
As most pipe materials have benefits and deficiencies, so do the joints that connect them. Also, while it may seem obvious, it is important to select materials and products that most effectively do the job required and to require proper installation techniques.
Since introducing its first patented product in 1968, EBAA has continued to lead the way in innovative products for the water and wastewater industry that are engineered to save time and money. EBAA is the only manufacturer of the world famous MEGALUG® Mechanical Joint Restraint. EBAA specializes in water and waste-water pipeline joints and is 100% MADE IN THE USA.